Participants in the 2019 cohort the Cambridge Executive MBA programme have implemented rapid changes within their respective organisations to respond to issues related to the COVID-19 (coronavirus) crisis.
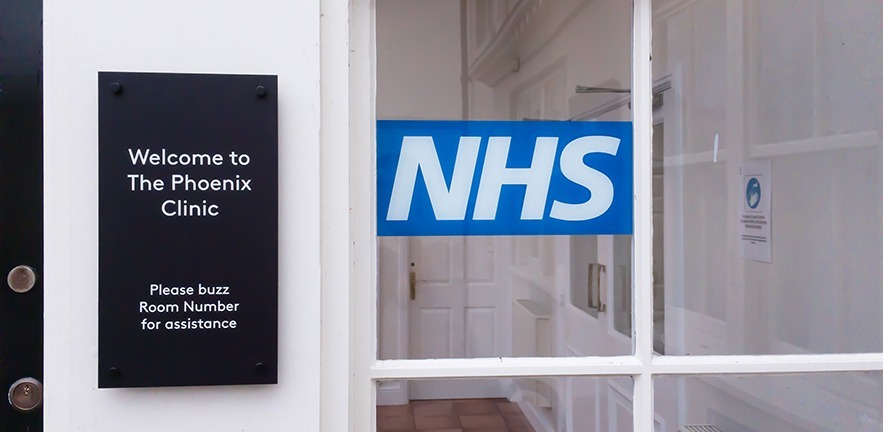
By considering how they can adapt organisational assets, utilise professional competencies and leverage networks, participants are approaching challenges with determination to save lives and livelihoods. From providing space for NHS health centres to pivoting to personal protective equipment (PPE) production, the Cambridge Executive MBA (EMBA) community is making a difference to support patients and workers.
Providing clinical space for the NHS
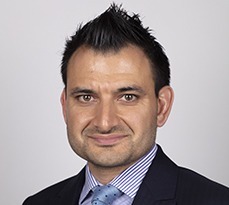
In response to increased demand for temporary clinical space to support patients during the COVID-19 crisis, Tariq Shah (EMBA 2019)’s company, Vigo Group, has transformed part of one of the company’s flexible office space centres into a fully refurbished and equipped health centre.
Vigo Group is a third-generation family business that specialises in investment, construction, and development of commercial and residential properties. The new health centre, The Phoenix Clinic, is the result of the commitment of the NHS and local businesses to work together in partnership and provide facilities to support patients during the current coronavirus crisis. Ahead of the transition, Vigo Group faced several challenges in its ambition to repurpose the space. Foremost, the fact that the space was currently occupied by businesses.
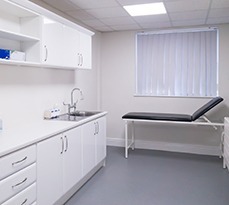
“We reached out to occupiers by telephone, and they were all very supportive of the initiative and bringing our local community together in the crisis,” said Tariq, based in Doncaster, where the new health centre is located. “There were practical and logistical concerns for each occupier that our management team, in collaboration with Doncaster Clinical Commissioning Group, were able to resolve quickly.”
The space was already designed for clinical use, but Vigo Group had to ensure it met Care Quality Commission (CQC) standards.
“To avoid unnecessary delay, we worked directly with clinicians to understand and implement alterations to meet the CQC’s standards. Examples of refurbishments included sourcing and installing hands-free tapes and basins, adjusting wayfinding signage and changes to the reception areas and emergency exits to reduce the risk of cross-contamination.”
Pivoting to PPE production
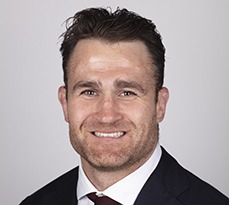
The production, procurement and distribution of PPE is a foremost consideration for companies and organisations employing frontline workers. As limited service, retail and pharmaceutical product providers remain open in many areas, a stretched supply chain is calling for innovation.
When the EGR Group, an Australian manufacturer of rigid polymer sheeting used in the automotive industry, realised the COVID-19 crisis would leave it with lots of gaps in its production schedule, it decided to evaluate how its products could be used to protect frontline workers.
James Horwill (EMBA 2019), the company’s Director for Strategic Planning, tells us about how everything changed for EGR after the unprecedented pandemic broke out.
“We’re the only company in Australia that manufactures this type of material on a mass scale. We already produce thousands of tonnes of plastic sheeting a year for the automotive industry in Australia and globally,” says James.
“Agility is important in any industry as you either adapt or die; for us, this was the case. With the automotive industry coming to standstill, we needed to quickly come up with new ways to keep our business operating, provide these much-needed resources for essential workers and job security for our staff.”
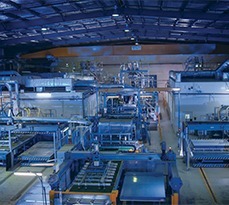
EGR made the rapid decision to start producing the face shields and protective screens needed by vulnerable key workers. With capacity to produce 25,000 face shields a day and with plans to scale up to more than 100,000 units a day by the end of May, EGR is playing an important role in the immediate supply chain and for future stockpiles.
“Traditionally our business has been B2B and not required a strong public presence. This shift in product, has meant we have had to evolve the way we approach our marketing. As a result, we are in the process of building a stronger online presence to reach those who are most in need.”
“We see benefits beyond Coronavirus to first responders and are looking to create a new medical division to supply the local health industry into the future.”
Prioritising testing and treatment drug development
While some organisations work to slow the reproduction of the virus, others are working to diagnose and treat those that have, or have had, it. One of those at the forefront of this effort is Swiss pharmaceuticals and diagnostics healthcare company, for whom Executive MBA participant Filipe Lope (EMBA 2019) works.
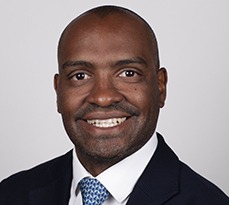
Facing the global healthcare crisis, Roche has committed to initiating and accelerating projects to build diagnosis and treatment capacity.
Filipe is a Project Leader in drug research & development, working with multi-functional expert teams driving the evaluation of new chemical entities and therapies.
“The therapies my teams are developing have the potential to become novel drugs to treat COVID-19,” says Filipe, who is based near Roche’s headquarters in Basel, Switzerland.
“Roche has already developed two relevant tools that are helping the diagnosis of COVID-19 in humans, namely the SARS-CoV-2 test which helped countries like Germany implement their COVID-19 testing strategy.”
Like many, Filipe is adapted to remote leadership, ensuring his teams stay motivated to hit targets from home.
“Most of the tools I need to do my job are accessible. Nevertheless, I’ve adapted my leadership style to ensure I’m transmitting a message of optimism to assuage anxieties and providing opportunities for frequent and open dialogues. Priorities established before the crisis have changed, and so I am reassuring colleagues that it’s understandable to face setbacks and overcome them constructively.”
“As a professional, this crisis is showing me a resilient side that I did not know I had before and I have figured out that in my case, in order to be efficient at work, it is not only how I manage my time but also about how I manage my energy.”